DEVELOPING A COST SAVINGS PROGRAM
Are you experiencing rising fuel system maintenance costs or higher than normal equipment failures? Consider the fact that studies repeatedly show fuel delivered to end users to be out of spec, containing unacceptable levels of contamination. Additionally, fuel ages and fuel systems breathe resulting in higher levels of contamination. Implementing a fuel quality management program (FQM) might be the cost savings answer you are looking for. In our last three articles we discussed the problems associated with fuel system contamination and considered some of the solutions. Now let’s put it all together in a program that will reduce your costs, liabilities and downtime.
FQM does not have to be overly complicated or costly. A three-step process is all it takes. It can be as simple as test, treat and protect. It is a risk assessment approach to fuel system maintenance that identifies problems and seeks cost-effective solutions.
Bacon Bomb Fuel Sampler
The first step – TEST – sample fuel and test to determine quality and set a baseline for further action. One of the most helpful tools a fuel system owner can have is a fuel sampler. Without a cross-section of fuel samples, it is virtually impossible to assess what is happening inside your fuel system. Open style dippers are inadequate for pulling acceptable samples from different fuel levels. In order to have a more complete picture of fuel quality, several samples should be taken from different access points and different levels within the fuel. The diagram below displays several potential locations. Ideally, a minimum of six samples should be taken from available access points in the tank.
Samples should be taken in clean, clear jars. Once collected, complete a simple visual test. Bottom samples are usually the most telling when taken from the lowest possible access point in the tank. If the sample contains biomass, water, particulates or dark aged fuel the risk is obvious – you have contaminated fuel that needs to be remediated. If the mid and upper layers are visually bright and clean looking, then it may only require pumping off the bottom contamination and treating the remainder of fuel with a biocide. If the all samples are clear, then additional testing for the presence of microbes will serve to confirm minimal contamination levels.
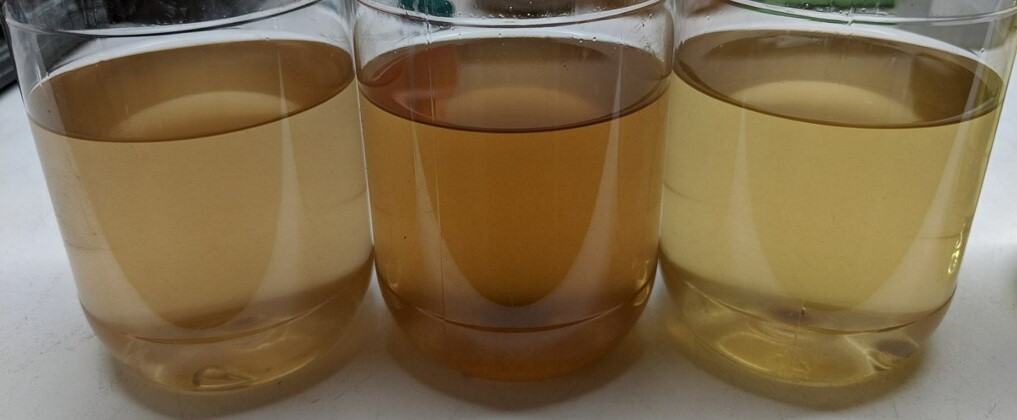
Unlike high volume facilities, fuel stored in a long-term storage facility require additional testing in order to reduce risk and potential contamination related cost. Two prime examples, back-up fuel generator systems or agricultural systems that operate during the growing season leaving fuel systems dormant during the rest of the year, are highly susceptible to aging. The longer fuel sets, the more opportunity there is for age related issues. Oxidization is part of the natural process. Hydrocarbon molecules exposed to oxygen break apart over time clogging filters, forming wax, asphaltenes and gums on the tank walls, probes and pumping equipment. Extreme weather and moisture exacerbate the process, especially when free water is present. Microbial growth is often unchecked and out of control. Test your fuel to determine the problems, including:
- Microbial Field Testing: Microbial testing can be completed quite easily in the field. If test results are required immediately, use FUELSTAT Plus the only ASTM Certified field test for microbial contamination with accurate results in minutes. If time and cost savings is a factor, Biobor’s Hum-Bug Kit is a low-cost, easy-to-use warning system that will effectively identify microbial contamination in all hydrocarbon fuels and oils. Even if fuel looks bright and clear, it still contains minimal levels of contamination. An early warning test will ensure fuel quality, prevent fuel waste and lower operational costs. Microbial testing should be a part of any FQM program.
- Water and Acid Content Field Testing: Additional testing can reveal hidden problems. Again, fuel can appear clean and yet still have enough water or a high enough acid level to increase costs and problems. If the visual bottom samples show moderate to high levels of contamination, studies show the likelihood of unacceptable levels of both. Field testing to determine water PPM or acid level may be warranted, especially with long-term fuel storage. These tests are low-cost and provide verifiable results to warrant further testing and treatment.
- Lab Testing: Testing for total fuel quality is an option not often used in the retail fuel industry. However, in the healthcare, generator back-up and heavy construction industry additional testing is often required or necessary. Poor fuel quality has been the primary cause of engine failure during emergency events. Diesel engines cannot run efficiently or at all on bad fuel. FQM is the cornerstone for risk assessment and cost reduction. Testing for total fuel quality can circumvent engine failure in an emergency event. Testing also provides helpful information used to diagnose engine related issues, potentially reducing future costs.
How does the fuel look? If it looks bad, it is bad. But what if the fuel looks good and you are still experiencing contamination related problems like slow-flow at the dispenser, prematurely clogged dispenser filters, ATG failure, accelerated hanging hardware failure or MIC? You may still have contamination issues. Fuel microbiologist, Dr. Fredrick Passman states “how the non-uniform distribution of microbes in fuels and fuel systems can make it challenging to collect a reliably diagnostic sample.” Visual inspections of both the fuel and fuel system help to paint a more complete diagnostic picture especially when maintenance is high and accessible fuel samples appear visually clean. The graph below can serve as a guide to risk assessment and FQM.
FQM Risk Assessment Graph
Bottom line, TREAT your fuel. FQM includes the proper use of biocides. Treating your fuel is not an option. Microbes live in the air, soil, and in fuel systems. Tanks systems vent, breathing in solid contaminants including microbes. Microbes are passed along the transportation system all the way to the end user. Unless something is done to stop and kill them, they are present and multiplying. Clean fuel systems are not possible without the use of biocides. Is it worth taking a chance? If you are not already on a biocide program then you have microbial contamination. The minimal cost for to apply a quality biocide like Biobor JF is nominal compared to the costs associated with microbial contamination – MIC, increased fuel system damage, risk and liability.
Biocides are not the only way to treat fuel. When diesel fuel ages, it loses cetane, lubricity, essential detergents and stabilizers that need to be replaced. They can also be used to enhance performance and efficiency or overcome seasonal issues. Biobor offers a selection of quality additives designed for and endorsed by major OEMs.
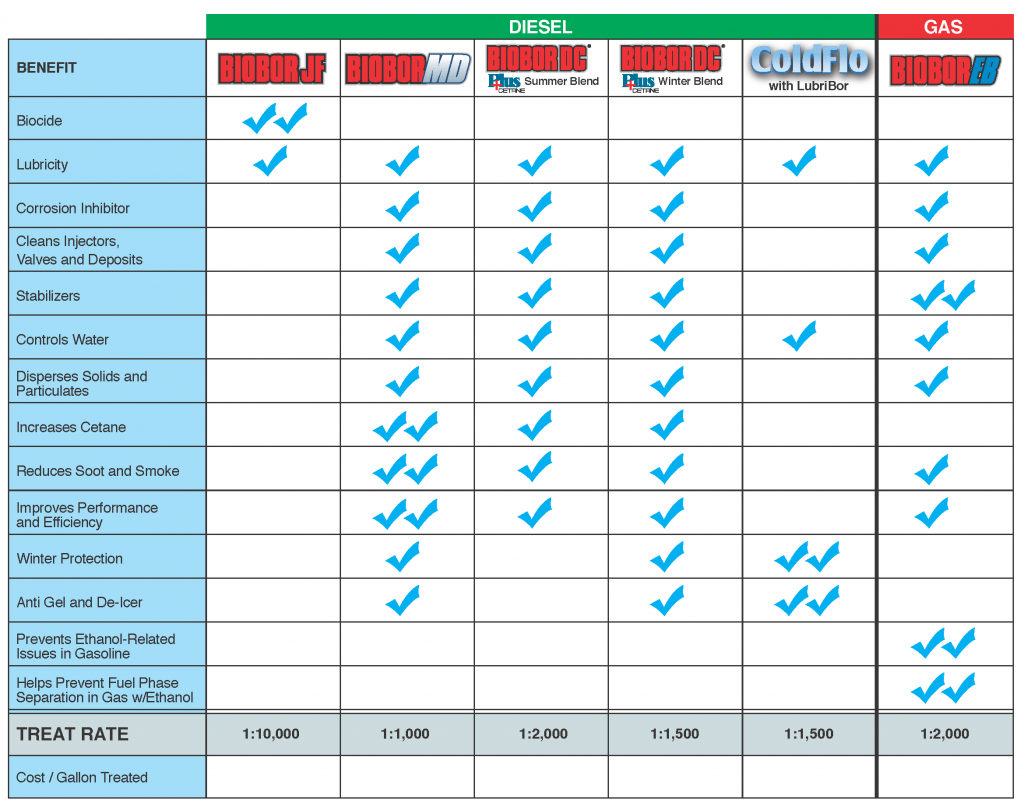
FQM is not a one-time event. It is an ongoing program aimed at reducing maintenance costs, liabilities and downtime. Once you TEST and TREAT, you must monitor your system and fuel – the PROTECT part of FQM. Consistent, periodic monitoring. Visual inspections and fuel sampling are all part of protecting your system from unwanted costs and problems.
The Biobor Fuel Quality Management Program is
- TEST = inspecting the fuel and system, testing the fuel for quality issues.
- TREAT = implementing a biocide treatment program and applying fuel additives as needed.
- PROTECT = monitoring the fuel and system for change.
Biobor products are the worldwide standard. Biobor®JF is the original, industry standard biocide since 1965, used in the most critical application – aviation. Independently tested, EPA registered and OEM approved for use in all hydrocarbons. It does not affect fuel performance and is more stable, less corrosive and safer to handle than other products. The Biobor family of products includes diesel fuel and gasoline additives designed to remediate, stabilize, clean and enhance fuel. If you manage fuel and fuel systems, and are not using additives as a way to reduce costs and liabilities contact the Biobor experts and find out how they can help you develop a personalize FQM program. If you are using non-Biobor products, contact us and find out why you need to make the change to Biobor.
Follow BioborShare the Post