In this final post on fuel system management, we will look at understanding fuel storage systems and the solution to providing clean, dry fuel as well as reducing fuel system maintenance costs. This is what we call:

A basic understand of the different types of fuel storage systems is the first step to fuel quality management (FQM). The anatomy of a fuel system varies from site to site. There are above ground storage tanks (AST) and underground storage tanks (UST) as well as specialty tanks of all kinds. Tanks can be vertical or horizontal. Some ASTs are tilted and have access for easy water drainage. The most difficult tanks to maintain are UST and baffled tank systems that offer limited access. A generator belly tank is one example. Even with a variety of types and applications, there are enough commonalities to draw accurate expectations. It is helpful to know that contamination is moved along the transportation system until it reaches the end user. Contaminants accumulate along the way resulting in higher maintenance costs. Understanding basic fuel system construction is the first step to cost reduction and FQM.
The generator belly tank might be one of the most challenging systems to maintain. Baffled tanks with very limited access for maintenance are some of the most difficult systems to maintain. Below is an illustration of a typical generator belly tank.
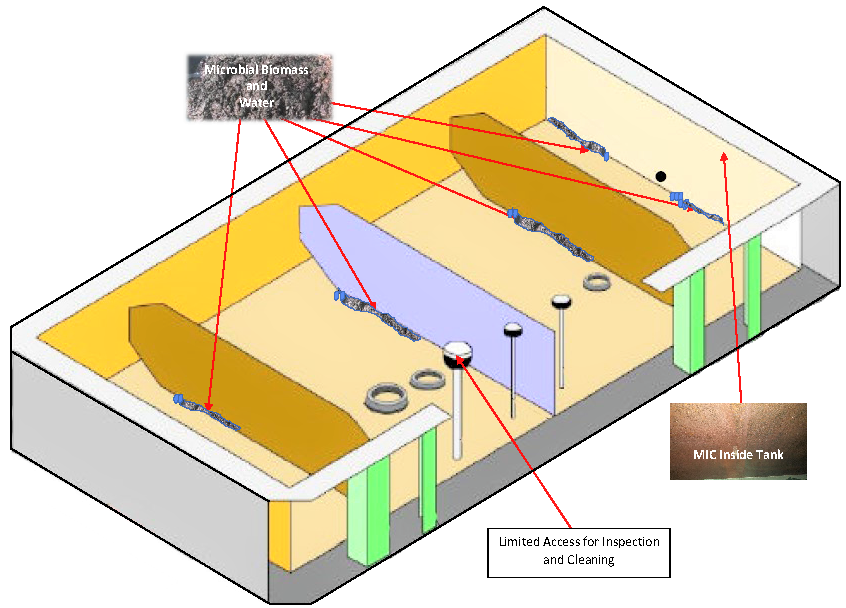
Notice the numerous places for water and microbial contamination to hide. With limited access, often a single fueling port, reaching contamination around baffles and through the tank is almost impossible. That is why tank cleaning is as much a creative art form as it is technical maintenance. The fuel cleaning technician has to be creative in finding ways to get the most out of the cleaning equipment and provide the best possible result. That is one of the reasons we have stressed the importance of using the right biocides and additives in our prior posts.
The illustration below shows a typical downstream application including tanks, access points, piping and pumping components where fuel quality problems occur.
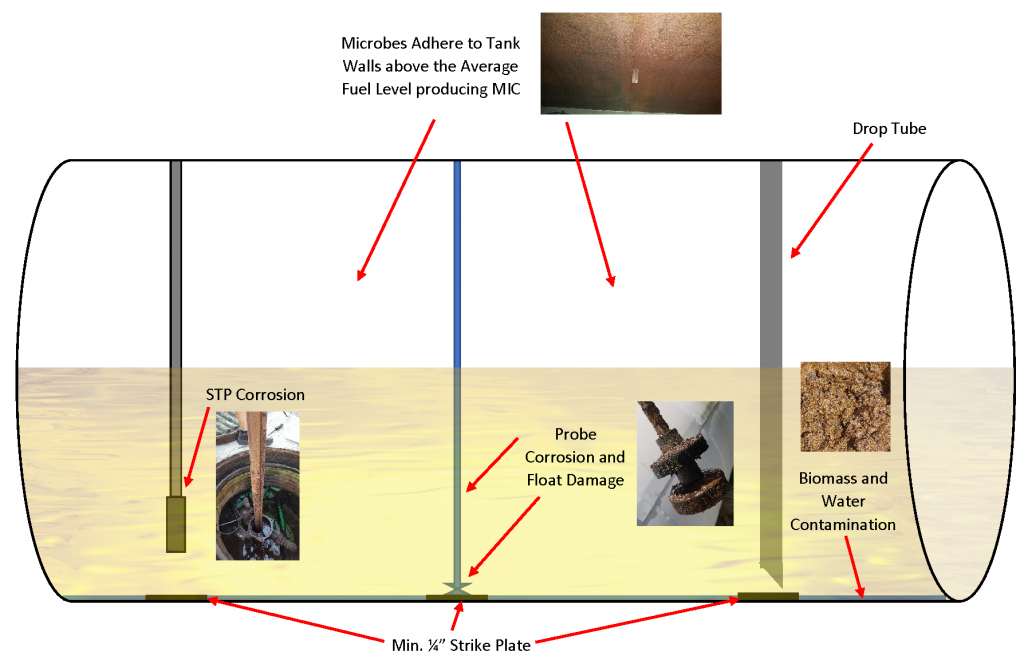
Application often dictates which type of tank system is used. Land cost, space availability and transportability as well as environmental factors play a role in determining the type. Whether an AST, UST or specialty tank, many of the components are the similar. No matter the type of tank, there are a 6 certainties that affect FQM:
6 Certainties that Affect Fuel Quality Management
- Water is always present in one form or another. All systems condensate. AST and generator systems are potentially more exposed to environmental changes than USTs. Extreme vacillations in temperature are not uncommon. Expect accelerated water accumulation and microbial growth in regions where temperatures are high. Knowing the type of tank and the conditions it is exposed to helps anticipate and identify potential problems.
- Tank strike plates and limited access create challenges for obtaining good fuel samples and identifying problems. Strike plates are typically a minimum of ¼” thick, most often found under access points. If you are sampling from an access point over a strike plate, then you may not identify water or other contamination until it rises above the strike plate. Limited access reduces your ability to view the tank condition and sample fuel inside of the tank without special, usually expensive equipment.
- USTs are not always level. They can settle over time or may be installed at an angle. Depending on the angle, free water and particulate contamination settle to the lowest end of the tank out of reach or sight. Knowing the tilt of a tank is important to FQM.
- Probe failure and false readings are not uncommon. Contamination damages probes and probe floats. Depending solely on automatic tank gauge systems is a mistake. There is no substitute for regular fuel sampling, testing and physical inspections.
- Drop tubes cause fuel agitation. When fuel is dropped, the drop tube will force the fuel and any settled contaminants away from product fills, agitating the contamination and moving it further from easy access. Sampling only from the fill can produce inaccurate results. It is always best to take multiple samples from as many access points as possible. Bottom, mid and top layer samples provide a more complete picture of the fuel tank environment.
- Beware of baffles. Tank baffles impede access and cleaning. They hide contamination and make it difficult, if not impossible to properly clean or regularly maintain the system. The image below is an example of a baffled tank with limited access.
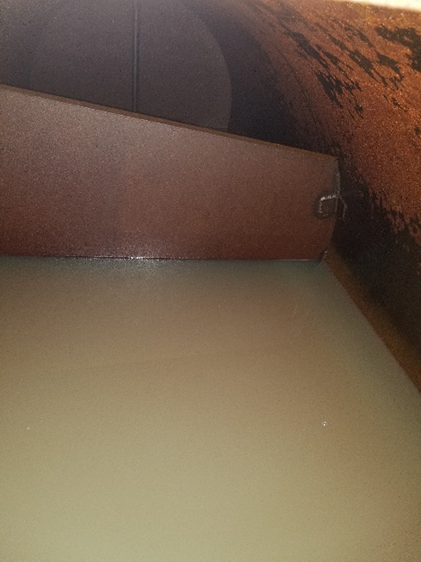
There are different types of piping ranging from rigid to flexible. They are made from steel, fiberglass, and polyethylene to name a few. No matter the type, construction and installation have a lot to do with how a system harbors contamination – especially microbiological growth (MBG). Any settling, dips or low points in a piping system offer a place for contaminants to collect and grow. Water collects and biofilms form in low spots. These places provide the perfect environment for MBG. Likely why the Coordinating Research Council report on diesel fuel storage and handling finds it is nearly impossible to properly maintain a fuel system without the use of biocides. The only way to reach pockets of microbial contamination deep within a fuel system is to apply a biocide to the fuel. The ideal biocide is Biobor®JF. Soluble in both fuel and water, it is carried along with the fuel throughout the system, killing MBG and partitioning into water when it is present. Test your fuel – good; Clean your fuel and tank – better; use Biobor®JF to maintain a clean system – best!

What is the solution to clean, dry fuel and proper equipment maintenance? Its as simple as TEST, TREAT and PROTECT.
3 Steps To Fuel Quality Management
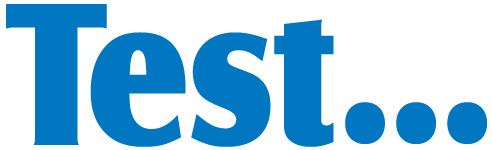
Sample and test the fuel for MBG using BIOBOR®Hum-Bug Detector® Kit or FUELSTAT® Plus. Identify free water and remove it immediately. Visually inspect the fuel. If it looks bad, it is bad. Use the below Visual Fuel Assessment Guide for help determining next steps
Test for MBG even if the sample looks good. Look for corrosion, another sign of MBG. The corrosion chart below was developed over years of field inspections, testing and treating microbial contamination. Use the Visual Corrosion Guide to identify MIC.
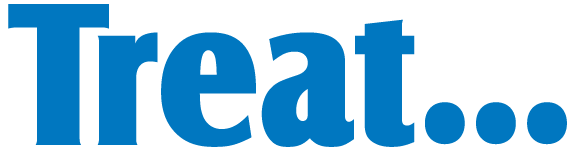
Clean and remediate your fuel using Biobor Fuel Additives. If you find microbes, contamination or aged and oxidized fuel, treat it. Treat your fuel with Biobor additives to improve fuel quality, equipment operability and efficiency.
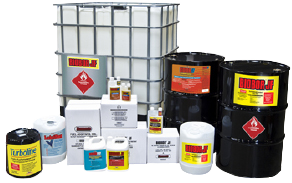
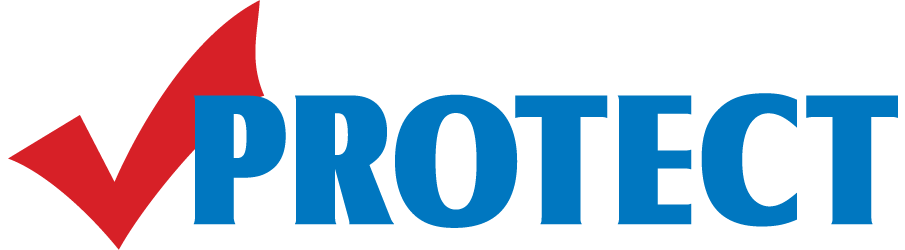
Monitor and maintain your fuel using Hammonds Test, Treat, Protect system. Perform monthly fuel sampling and biannual testing to identify changes in fuel quality. Treat your fuel quarterly with Biobor JF to reduce system corrosion and keep your fuel clean. Save on expensive maintenance costs by using Biobor JF and Biobor Fuel Additives.
Dirty fuel systems equal higher maintenance costs. If you do not have a FQM program in place, then you are already seeing the signs of neglect:
Signs of Fuel System Neglect
Fuel and Tank System Issues
- Premature filter replacements
- Corroded filters
- Meter corrosion
- Microbial Influenced Corrosion (MIC)
- Line and tank failure
- Line and tank failure
- Accelerated fuel aging
- Premature hanging hardware failure
- Shear valve failure (corrosion)
- Probe failure
- Dispenser over and under runs
Engine Issues
- Blocked filters
- Premature injector replacement
- Premature fuel system failure
- Fuel system leaks
- Faulty high pressure pump
- Engine failure
- Exhaust smoking heavily
- Lower engine efficiency
- Engine runs at lower RPM
- Engine runs rough or pings
- Low compression
Whether a fuel system or an engine, fuel quality is one of the most important maintenance items. It is also one of the most costly when ignored. Start today….. Call Hammonds Fuel Additives at 1-800-548-9166 or contact us.
Follow BioborShare the Post